US
Military are using smart metals similar
to those found at the Roswell Crash In
1947
"Time is ripe for the insertion of smart structures and materials
into space systems."
Dr. Keith
Denoger
Airforce Research
Laboratories
"Imagine seeing a
bullet shot through a sheet of material, only to have the material instantly
"heal" behind the bullet! Remember, this is not science fiction. Self-healing
materials actually exist, and LaRC scientists are working to unravel their
secrets.
What we did at NASA-Langley was
basically dissect that material to answer the question, 'how does it do that?'"
McGowan said. "By doing so, we can actually get down to computational modeling
of these materials at the molecular level. Once we understand the material's
behavior at that level, then we can create designer 'smart'
materials,"
Anna McGowan,
Program Manager for the Morphing
Project at NASA's Langley Research Center.
Does the above quote
sound familiar? Metal that is cut, only to 'heal' itself? We have all become
accustomed to hearing about technological advances that were initially
spearheaded by secret military research projects. The Atom Bomb was developed
during the Second World War amid incredibly tight security, and the first most
people knew about Stealth technology was when the bat-like fighter-bombers were
being rolled out of the hangers to attack the military apparatus of Iraq. Many
of us are expecting a new dawn of technological wizardry to make its debut
appearance during the current ‘war on terrorism’.
Cosmic
Conspiracies would like to share with you some remarkable information
relating to current cutting-edge technological research being conducted on
behalf of the U.S. military that we believe could be connected to the materials
found from the Roswell crash. We are stunned by it, not least because of how
freely available much of the data is on the Internet. Finding this freely
available material, however, is extremely difficult unless you are aware of the
specific keywords being utilised, or, as in our case, you have a researcher of
the calibre of Martin Cosnette. This is not common
knowledge, despite the amazing jump in technology implied by the rapid advances
being made right now.
Click on the picture below to see a simulation of what the smart materials will be used for.
Click to download Quicktime
Movie Player
Image courtesy of
Robert C. Byrd National Technology Transfer Center.
The
above picture is an artists impression that was drawn from witness' accounts
of the Roswell craft. We think its uncanny how similar it looks to the craft in the movie
simulation which was recently released by NASA! The image was drawn by William Louis McDonald and
taken from the book 'The Encyclopedia of Extraterrestrial Encounters', by Ronald
Story, 2001.
Amazing advances are being made in the development of new metal
alloys. These alloys have remarkable characteristics, in that they will change
shape upon the application of an electric current or magnetic field. They change
shape, or ‘morph’ as the researchers prefer to say, rapidly and with some
considerable force. They are termed ‘compact hybrid actuators’, a mouthful of
engineering jargon, so we would prefer to call them ‘living metals’. Why?
Because these alloys incorporate advanced nano-technology that is designed to
enable them to mimic living systems in their versatility and dynamism. The list
of potential applications seems endless, and the U.S. military is funding a
variety of related research programs exploring the full range of options.
Self-healing wings that flex and react like living organisms, versatile bombers
that double as agile jet fighters, and swarms of tiny unmanned aircraft are just
a few of the science-fiction-like possibilities that these next-generation
technologies could make feasible in the decades ahead.
Just so that you don’t
think this all sounds like drawing-board ideas being dreamt up by some egg-head
think-tank, there is a considerable body of evidence to show that the testing
stage for some of these alloys has already taken place.
We have accessed over 130
documents so far, including pictures and video footage, budgets and names of
project leaders and their departments/companies involved. This technology is
being incorporated into prototype applications right now. These include morphing
aeroforms in Unmanned Aerial Vehicles (UAVs) and fighter aircraft, morphing
rotor-blades in helicopters, in-flight navigation, guidance and control systems
for small missiles, satellite technology (especially with respect to optical
systems), and sonar-absorbing materials for submarines. If you watch the video
animation above, you will see that a plane with flappable wings is one of the
goals of this project.
These active and complex metal
alloys are being designed to be used in ‘exo-skeletons’ to be worn by
battle-field soldiers, creating ‘Robo-cop’ style advances in G.I. Joe’s combat
performance.
The U.S. Military are currently inviting applications for between
$30-40m of research grants to find ways of facilitating neural transmission
between the soldier’s brain waves and his living metal exo-skeleton. They are
not expecting mere ‘incremental’ progress, either. The projects are 3-year terms
in length, and many of them are nearing completion or are already accomplished.
There is a palpable sense of urgency to this research, and we think this
reflects the rapid advances being made in these projects.
The research is being
conducted by a number of private-sector aerospace consortiums (including the
likes of Boeing, M.I.T., Moog and Lockheed Martin), as well as several
university departments in receipt of grants from the U.S. Military.
The entire
project is being supported by the following military organisations: the US Army
Research Office, the Office Of Naval Research, NASA Langley Research Center
(yes, they’re military too!), and (wait for it…) the Space Operations Vehicle
Technology Office, AFRL/VAS at Wright Patterson AFB.
As you probably already
know, there's a hangar at Wright Patterson Air Force base that contains
very highly classified material, believed to be Roswell and/or other ET remains,
so tightly controlled that even Barry Goldwater, a US Senator and Major General
in the USAF Reserve, was denied access.We are intrigued by this final
link, as you will see in our discoveries below!
Other projects that
involve the shape memory alloys include vortex wake control (vortex tabs on
control planes), smart wings, smart skins (self and radiated noise cancellation)
smart panel (structure acoustic and vibration isolation) and they are to be used
in the construction of space laser weapons in the future.
Morphing Project Program Manager lets slip that the
smart materials they are working on could be back
engineered!
We were staggered at the
remarks on Langleys AFB website made by Anna McGowan, program manager for the
Morphing Project at NASA's Langley Research Center (which is a part of this
project, but not the main company).
She says:
"Among the exotic "smart" materials being developed by the
Morphing Project, shape-memory alloys are relatively ordinary. Imagine seeing a
bullet shot through a sheet of material, only to have the material instantly
"heal" behind the bullet! Remember, this is not science fiction. Self-healing
materials actually exist, and LaRC scientists are working to unravel their
secrets.
"What we did at NASA-Langley was basically dissect that
material to answer the question, 'how does it do that?'" McGowan said. "By doing
so, we can actually get down to computational modeling of these materials at the
molecular level. Once we understand the material's behavior at that level, then
we can create designer 'smart' materials," she added.
LaRC is also developing customized variations of piezoelectric
materials. These substances link electric voltage to motion. If you contort a
piezoelectric material a voltage is generated. Conversely, if you apply a
voltage, the material will contort.
The above statement seems
odd to us. Why would you strip down technology to see how it works if you had
built it in the first place? Or does this mean that NASA-Langley did not make
the material, but are in fact back-engineering it?
M o r p h i n g M e t a l
sWe've waited a little while before releasing
this information. That was partly because we wondered whether the head of
the Compact Hybrid Actuation Program (CHAP) would reply to our extensive
questions, and partly because of the following:
When we first made it known that we
thought we had come across something awesome to do with advanced ‘morphing
metal’ technology, there was some mention that this was already common
knowledge. We assumed, then, that other researchers and commentators, who
had questioned our judgement, would come forward with the references and data
that we had discovered, and ‘show us up’, as we say here in Britain.
Instead, we have had many people asking us when we’re releasing our data, and no
one showing us how this is an ‘old story’.
Now, we are not
omnipotent. There may be some people out there who know all about this
already, but the feedback we have received indicates that, to the vast majority
of people out there, this is entirely new material. No one else is carrying this
story except Cosmic Conspiracies. If that’s because they don’t think it’s
important, then that’s up to them. We have been interested in UFOlogy for
some considerable time, and read a lot of material, both in magazines and
on-line, and this material is news to us. We remain excited by it, not
necessarily because it individually blows the lid off the ‘seeding technology’
business between the US Military and private industry/academic research labs,
but because, taken in the context of the claims of Colonel Philip Corso and
others, it adheres to a pattern that is noticeable, and significant.
So we will leave it to others
whether this is news-worthy, or otherwise. We’ve given others the chance
to break this story if they think we are trawling over old ground, and they
haven’t. This is a story that we think should be heard. So here it
is…
These summaries of ‘morphing metal’
technologies have been gleaned from the extensive DARPA site, the cutting edge
research organisation that is part of the U.S. military. The
‘state-of-play’ that is described on the surface is incredible enough, but when
you start to dig a little deeper, and put a few connections together, the full
potential for this technology becomes self-evident.
1. "DARPA and the ARO have been
developing active control applications of smart materials and structures over
the last 6 years" (2000). So although this is a relatively recent programme
exploring the potential for these technologies, the degree of practical
application already managed would suggest an exciting level of success. The
DARPA organisation directs cutting edge research which is initially speculative,
with a high probability of failure, but also with the potential for occasional
bursts of brilliance.
2. The actuators currently used in
the wings of certain aircraft are facilitating 'morphing airfoil technology',
whereby the shape of the aero-form can be altered mid-flight to maximize a
particular manouevre or flight performance. "Adding the active
member into the control system significantly increases the controllability of
the torsional modes for a marginal (0.1%) increase in power."
Military researchers and developers are succeeding in making aero-forms with
wings that change shape with very little power usage, and no moving
parts.
So, in the case of a fighter
aircraft or UAV (Unmanned Aerial Vehicle), the variability of the shape of the
aero-form allows optimization for both 'subsonic interdiction' and also
'supersonic intercept missions'. In other words, an aircraft could assume one
shape for flying towards a mission target, then take on another form for
performing more rigorous manouevres when in action. This extends mission
performance significantly. This is well known in some quarters, although
it may still surprise many. But, from what we have been reading, we think
that this is the tip of the ice-berg!
The actuation devices enable
surfaces to be controlled without the need for a traditional steering mechanism
or driving hardware, increasing performance and structural stability. The
devices are electrically driven, delivering a high force potential quickly. In
practice, the shape of the wing actually re-contours whilst under significant
external stresses, and then returns to its rest position without displacement
after the applied electrical current has been stopped. In the case of missiles,
thin film shape memory alloys might be used in nose control systems as compact
navigation, guidance and control technologies.
3. Various alloys have been
developed that retain a shape memory. Some of these actuators perform
mechanically upon the application of a magnetic field only. For instance,
that NiTinol, Ni-free Titanium and ferromagnetic Smart Memory Alloys can be
"energized by [a] magnetic field". We think that this property may
certainly have a connection with UFO technology, insofar as it has been
generally reported; unidentified aero-forms that change shape mid-flight, and
have hazy appearances that relate to an energy field pervasive around the UFO at
the time. There are many magnetic anomalies reported by witnesses and
researchers, and a correlation between changing form and magnetic field effects
appears to be an important consideration.
4. A non-military application that
has been cited by CHAP researchers (who may be anxious to see their research put
to some beneficial use) is in the use of Braille. We understand this to mean
that 'writing' could be induced upon a smooth metallic surface, that can then
return to its flattened states for continual reuse. One can then imagine a
scrolling metallic script upon a metal interface that will allow Braille readers
to access, say, an electronic book with ease. It is a wonderful
possibility.
5. It is mentioned that the
architectures of the actuators are complex, and an allusion to an ‘organic
system’ is given when talking about some of these remarkable metal alloys.
Upon the stimulus of an external command the powered actuator will be able to
produce a mechanical force autonomously, and respond to a degree of complexity
hitherto unimagined. Given the incredible leaps in information technology
that have been made over the past couple of decades, the level of command detail
for a ‘morphing metal’ is very great indeed. If they are as adaptive as is
being reported in the scientific papers, then their flexibility could certainly
mimic living systems, like muscles. For instance, this quote is made by
the Sarcos research team:
"These new actuators are similar
in architecture to biological systems (elements arranged in parallel-series
assemblies), but use very different building blocks. As in biological systems,
the individual elements are optimized for best performance around one operating
point…
"The small
elements forming these actuation system achieve high power and energy density by
using combustible fuel energy sources and efficient energy conversion via
oscillatory and sometimes resonant processes. The power produced by the sources
will be modulated at the individual element level rather by means of lossy
components such as valves and power transistors, thereby providing power on
demand with low power quiescent state. By using a modular architecture where
many similar or identical elements are used, mass production methods becomes
possible and economies of scale can be achieved. This approach, which we
designate as Organismic Systems, is characterized by the use of many elements
which are systematically interconnected in terms of structure, physical effort,
and information."
The power to drive the actuators is
portable, and could, for instance, take the form of a back-pack worn by soldiers
who are powered lower body exoskeletons. But there are hints in the
research texts alluding to truly 'intelligent' materials. We consider it likely
that the modular architecture described fits in with the general concepts of
'nano-technology'. That is, the intelligent ‘biological’ actuators have
purpose-built machines within it designed at the molecular level.
This then takes on an altogether
new dimension when placed in the context of proposed brain implants that can
pick up neurological information directly. This information could then
readily be transferred to the ‘morphing metal’ interface that will be quite
capable of adapting to the complex commands delivered by the brain. One
can imagine the development of prosthetic limbs made of these alloys that
receive direct instruction from the wearer’s brain, and therefore react like
real limbs. The military applications are obviously quite incredible, and
this might very well explain why $30-40m of military funding is up for grabs to
develop this kind of neuro-control technology.
6. Finally, compact hybrid actuators are
being developed to reduce levels of self-noise, particularly with respect to the
sonar detectibility of torpedoes. Mention is also made of Unmanned Underwater
Vehicles (I presume this is what is meant by UUV's). This technology seems
to represent a kind of 'stealth' characteristic for underwater vehicles and
weapon systems. One wonders whether a similar system has been applied to ground
or air vehicles to effectively 'cloak' them on an auditory level?
Certainly, it is known that there
are ‘silent’ helicopters, and ground vehicles used by special forces units that
have stealth characteristics.
These current applications might
lead us to suspect that the progress in this technology that has been officially
released by DARPA, and the ‘actual’ state of play are two entirely separate
things. This will not be a surprise to anyone, of course, and one would
expect the U.S. Military to keep their latest leaps in technology under wraps
for when they are actually needed. But this could certainly indicate that
what we are presenting as ‘state-of-the-art’ in morphing metals is actually
nothing of the kind. Which then allows us to consider the ‘proposed’
future advancements with just a little scepticism. Are we simply being
‘drip-fed’ with information about remarkable leaps in material technologies that
are just around the corner?
Think about it…why are DARPA making
all this information publicly available when these projects represent
cutting-edge military research and development? They didn’t do that with
Stealth. We think there is much more to come, but you can take a look and
judge for yourself. Become informed, because we think this ‘material’ will
become a big part of your life sooner than you think…
Shape Memory
Alloys
As incredible
as it sounds, material scientists conducting research projects for the American
military are successfully creating metals that can not only change shape upon
the application of an energy field, but that might soon be able to autonomously
‘self-actuate’! Are we on the verge of creating intelligent alloy
materials that have their own memory and motion capabilities? Is this
scientific progress an indirect result of the now infamous exotic materials that
once fell into the hands of the US Government in 1947?
The following executive report explains the state
of the art ‘intelligent material’ science produced by a University of
Washington-based research group for CHAP, a highly ambitious materials research
project commissioned by DARPA, the Defense Advanced Research Projects
Agency:
Development of Compact Hybrid Actuators Based on
Ferromagnetic Poly-crystal Fe-Pd Material
“The goal of the UW-Instron-DOE Albany project
is the design of a robust compact actuator based on polycrystalline
ferromagnetic shape memory alloy (FSMA) materials. " New materials will also
be investigated. A preliminary study of a proof-of-concept device has been
completed and is described below:
“…The ductile nature of the polycrystalline
Fe-Pd allows it to be processed into any 3-D shape, including springs, by using
conventional processing methods, which would be quite cost effective.
[There is a] rapid actuation of the polycrystalline Fe-Pd spring driven by a
portable magnet: the large stroke achieved with application of the magnetic
field is clearly seen. In this project, a more compact electromagnetic
system housed inside the Fe-Pd spring will be developed. In addition, new
material compositions will be investigated, including Fe-Pd-Pt for a more
noticeable shape memory effect and better superelasticity behavior and
Fe-Ti-Co-Ni for cost.
“After improving the performance of the Fe-Pd
spring actuator, a proto type will be built and demonstrated for Phase 1.
The prototype unit will consist of a Fe-Pd spring actuator (L=15cm, dia=3cm), an
electromagnetic driving unit to be housed inside the spring, and a position
sensor with a central unit. This device is expected to provide up to a
10cm stroke capability with a relatively large force (150N).”
In a response to: Solicitation BAA00-03: Compact
Hybrid Actuation Program (CHAP)
Prime
Contractor: University of Washington
Dr.
Minoru Taya, PI, Professor and Director
Center for Intelligent Materials and System
Department of Mechanical Engineering
University of Washington
These Iron-Palladium alloys are clearly capable of
remarkable shape-changing feats already. The investigating team is now
attempting to integrate further ‘intelligent’ components into the alloy, such
that there will be no requirement for an external energy field to be applied to
the metal to make it reshape. Is this nano-technology at work? The
metal itself will incorporate an ‘electromagnetic driving unit’ and, presumably,
a ‘position sensor with a central unit.’
How large is the Fe-Pd spring actuator? Just 15cm
length by 3 cm diameter. Yet this spring will become an intelligent
autonomous machine with a remarkable tensile strength and stroke
capability. It will have its own ‘shape memory’.
Where have we heard of this kind of exotic
material before? Before answering this question, let us explore the nature
of these remarkable new materials a little more.
The Sarcos research team describes these new forms of
actuator in this way:
“These new actuators are similar in
architecture to biological systems (elements arranged in parallel-series
assemblies), but use very different building blocks. As in biological systems,
the individual elements are optimized for best performance around one operating
point…
“The small elements forming these actuation
system achieve high power and energy density by using combustible fuel energy
sources and efficient energy conversion via oscillatory and sometimes resonant
processes. The power produced by the sources will be modulated at the individual
element level rather by means of lossy components such as valves and power
transistors, thereby providing power on demand with low power quiescent state.
By using a modular architecture where many similar or identical elements are
used, mass production methods becomes possible and economies of scale can be
achieved. This approach, which we designate as Organismic Systems, is
characterized by the use of many elements which are systematically
interconnected in terms of structure, physical effort, and
information.”
In other words, these metals are essentially
machines that are built at the elemental level, and have complex internal
architecture and systems in a similar way to living ones. The
nano-machines incorporated into the metal alloys utilize energy sources at the
‘individual element level’. The metal alloy actuators are essentially
autonomous. This is very remarkable indeed, particularly given the
accounts of those who have come into contact with materials alleged to be of an
extra-terrestrial nature.
The Roswell
Artifacts
In the
latest research update by Thomas J. Carey & Don R. Schmitt regarding the
Roswell case, they describe up to 9 types of exotic materials variously reported
by witnesses to the events of July 1947 in New Mexico. One of these types
of metal has particular relevance here:
“An unknown quantity of very small to
hand-sized pieces of a very thin and very light “metal” that displayed both
solid and “fluid” qualities. The colour of dull aluminium, a piece of it
could be wadded up like a ball in one’s hand [without any sensation of weight]
and, when placed on a flat surface, it unfurled [“flowed like water”] to its
original flat, seamless shape without a mark on it. Also extremely tough,
it could not be cut, scratched or burned.
“Note: it is this so called ‘memory metal’ that
our investigation today refers to as the ‘Holy Grail’ of Roswell since a piece
of it, if found, would in our view constitute irrefutable proof that an
extraterrestrial spacecraft had been recovered.” (UFO Magazine
Sept/Oct 2000 p62)
Perhaps, if the CHAP project continues to make the
rapid progress that it has been in recent years, such material might not be
solely the domain of extra-terrestrial visitors to our planet. Could
Compact Hybrid Actuators be the terrestrial equivalent of the Roswell
artifacts? Indeed, is it possible that the various research organisations
engaged in the production of this kind of material are being surreptitiously
guided towards this outcome? Perhaps there are good reasons for believing
so…
Colonel
Corso
In his controversial book ‘The Day After Roswell’
Col. Philip J. Corso (Ret.), the former head of the Foreign Technology Desk at
the U.S. Army’s Research and Development department, described his own
experience of examining similar material alleged to come from the 1947 crash
site:
“There was a dull, greyish-silvery foil-like
swatch of cloth among these artifacts that you could not fold, bend, tear, or
wad up but that bounded right back into its original shape without any
creases. It was a metallic fibre with physical characteristics that would
later be called “supertenacity,” but when I tried to cut it with scissors, the
arms just slid right off without even making a nick in the fibres. If you
tried to stretch it, it bounced back, but I noticed that all the threads seemed
to be going in one direction. When I tried to stretch it width-wise
instead of length-wise, it looked like the fibres had re-orientated themselves
to the direction I was pulling in. This couldn’t be cloth, but it
obviously wasn’t metal. It was a combination, to my unscientific eye, of a
cloth woven with metal strands that had the drape and malleability of a fabric
and the strength and resistance of a metal. I was on top of some of the
most secret weapons projects at the Pentagon, and we had nothing like this, even
under the wish-list category.” (The
Day After Roswell, p49 Pocket Books 1997)
Although this appears to be a variant on the
metallic artifacts reported by Roswell witnesses, Corso’s account is no less
interesting for that, particularly given his claims about what happened to this
material. In keeping with his own role as the ‘seeder’ of the Roswell
technologies to the giants of American industry, the ‘supertenacious fibres’
allegedly found there way to the research departments of Monsanto and Dow
(p235). Furthermore, Corso claims that the material had previously been
delivered to the Air Materiel Command at Wright Field (p236). Wright
Patterson Air Force Base, as it is now known, is famous in UFO circles for its
Foreign Technology division, purported to hold extra-terrestrial craft and
artifacts (See ‘Above Top Secret: The Worldwide UFO Cover-up by Timothy Good,
1988).
Department of
Defense Collaborator
Given this persistent rumour about the hidden work
conducted at Wright Patterson AFB, then it is certainly quite remarkable that
this particular base should feature among a select band of DoD collaborators for
the CHAP research:
“Several other Department of Defense (DoD)
agencies conduct research related to DARPA's work in the area of Compact Hybrid
Actuators. The following DoD collaborators serve as information resources to the
program, promoting knowledge sharing among research teams:
1. Gary L. Anderson
US Army Research Office
2.
3. Roshdy
George S. Barsoum, PhD, PE
Office Of Naval
Research
4. David B. Homan, Deputy Program Manager
Space Operations Vehicle Technology Office
AFRL/VAS
Wright Patterson AFB,
5. Garnett Horner
NASA Langley Research Center”
Does the role of the ‘Space Operations Vehicle
Technology Office’ at Wright Patterson AFB here specifically involve ‘seeding’
information about ‘memory metals’ to the CHAP research teams? This must be
a strong possibility.
UPDATE September
2002
It seems that
the CHAP project is steaming away at full power since we first learnt of
it in December, 2001. This article was posted recently on NASA's
research site at http://www.ipt.arc.nasa.gov/spacetransport.html
We
thought you would enjoy reading the new developments, including plans
for space vehicles to be able to repair themselves mid-flight. Don't say
we didn't tell you so!
Dave
at Cosmic Conspiracies...
Revolutions in technology--like the
Industrial Revolution that replaced horses with cars--can make what
seems impossible today commonplace tomorrow.
Such a revolution is happening right now. Three of the fastest-growing
sciences of our day--biotech, nanotech, and information technology--are
converging to give scientists unprecedented control of matter on the
molecular scale. Emerging from this intellectual gold-rush is a new
class of materials with astounding properties that sound more at home in
a science fiction novel than on the laboratory workbench.
Imagine, for example, a substance with 100 times the strength of steel,
yet only 1/6 the weight; materials that instantly heal themselves when
punctured; surfaces that can "feel" the forces pressing on
them; wires and electronics as tiny as molecules; structural materials
that also generate and store electricity; and liquids that can instantly
switch to solid and back again at will. All of these materials exist
today ... and more are on the way.
With such mind-boggling materials at hand, building the better
spacecraft starts to look not so far fetched after all.
Weight equals money
The challenge of the
next-generation spacecraft hinges on a few primary issues. First and
foremost, of course, is cost.
"Even
if all the technical obstacles were solved today, exploring our solar
system still needs to be affordable to be practical," says Dr.
Neville Marzwell, manager of Revolutionary Aerospace Technology for
NASA's Next Decadal Planning Team.
Lowering the cost of space flight primarily means reducing weight. Each
pound trimmed is a pound that won't need propulsion to escape from
Earth's gravity. Lighter spaceships can have smaller, more efficient
engines and less fuel. This, in turn, saves more weight, thus creating a
beneficial spiral of weight savings and cost reduction.
Right: This fully-loaded Saturn V
moon rocket weighed 6.2 million pounds. It was heavy and expensive to
launch. [more]
The challenge is to trim weight while increasing
safety, reliability, and functionality. Just leaving parts out won't do.
Scientists are exploring a range of new technologies that could help
spacecraft slim down. For example, gossamer materials--which are
ultra-thin films--might be used for antennas or photovoltaic panels in
place of the bulkier components used today, or even for vast solar sails
that provide propulsion while massing only 4 to 6 grams per square
meter.
Composite materials, like those used in carbon-fiber tennis rackets and
golf clubs, have already done much to help bring weight down in
aerospace designs without compromising strength. But a new form of
carbon called a "carbon nanotube" holds the promise of a
dramatic improvement over composites: The best composites have 3 or 4
times the strength of steel by weight--for nanotubes, it's 600 times!
"This
phenomenal strength comes from the molecular structure of nanotubes,"
explains Dennis Bushnell, a chief scientist at Langley Research Center (LaRC),
NASA's Center of Excellence for Structures and Materials. They look a
bit like chicken-wire rolled into a cylinder with carbon atoms sitting
at each of the hexagons' corners. Typically nanotubes are about 1.2 to
1.4 nanometers across (a nanometer is one-billionth of a meter), which
is only about 10 times the radius of the carbon atoms themselves.
Left: The lattice of carbon atoms in a carbon nanotube is
like a peg-board for hanging other kinds of atoms and molecules to give
the nanotube special chemical, electrical or thermal properties.
Copyright Prof.
Vincent H. Crespi Department of Physics Pennsylvania State
University. [more]
Nanotubes were only discovered in 1991,
but already the intense interest in the scientific community has
advanced our ability to create and use nanotubes tremendously. Only 2 to
3 years ago, the longest nanotubes that had been made were about 1000
nanometers long (1 micron). Today, scientists are able to grow tubes as
long as 200 million nanometers (20 cm). Bushnell notes that there are at
least 56 labs around the world working to mass produce these tiny tubes.
"Great strides are being made, so making bulk materials using
nanotubes will probably happen," Bushnell says. "What we don't
know is how much of this 600 times the strength of steel by weight will
be manifest in a bulk material. Still, nanotubes are our best bet."
Right:
The tensile strength of carbon nanotubes greatly exceeds that of
other high-strength materials. Note that each increment on the vertical
axis is a power of 10. [more]
Beyond merely being strong, nanotubes
will likely be important for another part of the spacecraft weight-loss
plan: materials that can serve more than just one function.
"We used to build structures that were just dumb, dead-weight
holders for active parts, such as sensors, processors, and
instruments," Marzwell explains. "Now we don't need that. The
holder can be an integral, active part of the system."
Imagine that the body of a spacecraft could also store power, removing
the need for heavy batteries. Or that surfaces could bend themselves,
doing away with separate actuators. Or that circuitry could be embedded
directly into the body of the spacecraft. When materials can be designed
on the molecular scale such holistic structures become possible.
Spacecraft skins
Humans can feel even the slightest
pinprick anywhere on their bodies. It's an amazing bit of
self-monitoring--possible because your skin contains millions of
microscopic nerve endings as well as nerves to carry those signals to
your brain.
Likewise, materials that make up critical
systems in a spaceship could be embedded with nanometer-scale sensors
that constantly monitor the materials' condition. If some part is
starting to fail--that is, it "feels bad"--these sensors could
alert the central computer before tragedy strikes.
Molecular
wires could carry the signals from all of these in-woven sensors to the
central computer, avoiding the impractical bulk of millions and millions
of today's wires. Again, nanotubes may be able to serve this role.
Conveniently, nanotubes can act as either conductors or semi-conductors,
depending on how they're made. Scientists have made molecular wires of
other elongated molecules, some of which even naturally self-assemble
into useful configurations.
Above: This piezoelectric
material, developed at NASA's Langley Research Center (LaRC), can
"feel" deformations such as bending or surface pressure,
producing a small voltage in response that can act as a signal for a
central computer. Image courtesy NASA's Morphing Project at LaRC.
Your skin is also able to heal itself. Believe it or not, some advanced
materials can do the same thing. Self-healing materials made of
long-chain molecules called ionomers react to a penetrating object such
as a bullet by closing behind it. Spaceships could use such skins
because space is full of tiny projectiles--fast-moving bits of debris
from comets and asteroids. Should one of these sand- to pebble-sized
objects puncture the ship's armor, a layer of self-healing material
would keep the cabin airtight.
Meteoroids aren't the only hazard; space is filled with radiation, too.
Spaceships in low-Earth orbit are substantially protected by our
planet's magnetic field, which forms a safe bubble about 50,000 km wide
centered on Earth. Beyond that distance, however, solar flares and
cosmic rays pose a threat to space travelers.
Right:
A solar flare blasts energetic radiation into space. [more]
Scientists are still searching for a good
solution. The trick is to provide adequate shielding without adding lots
of extra weight to the spacecraft. Some lightweight radiation-shielding
materials are currently being tested in an experiment called MISSE
onboard the International Space Station. But these alone won't be
enough.
The real bad guy is Galactic Cosmic
Radiation (GCR) produced in distant supernova explosions. It consists,
in part, of very heavy positive ions--such as iron nuclei--zipping along
at great speed. The combination of high mass and high speed makes these
little atomic "cannon balls" very destructive. When they
pierce through the cells in people's bodies, they can smash apart DNA,
leading to illness and even cancer.
"It turns out that the worst materials you can use for shielding
against GCR are metals," Bushnell notes. When a galactic comic ray
hits a metallic atom, it can shatter the atom's nucleus--a process akin
to the fission that occurs in nuclear power plants. The secondary
radiation produced by these collisions can be worse than the GCR that
the metal was meant to shield.
Ironically, light elements like hydrogen
and helium are the best defense against these GCR brutes, because
collisions with them produce little secondary radiation. Some people
have suggested surrounding the living quarters of the ship with a tank
of liquid hydrogen. According to Bushnell, a layer of liquid hydrogen 50
to 100 cm thick would provide adequate shielding. But the tank and the
cryogenic system is likely to be heavy and awkward.
Here
again, nanotubes might be useful. A lattice of carbon nanotubes can
store hydrogen at high densities, and without the need for extreme cold.
So if our spacecraft of the future already uses nanotubes as an
ultra-lightweight structural material, could those tubes also be loaded
up with hydrogen to serve as radiation shielding? Scientists are looking
into the possibility.
Above: When high-energy
cosmic rays crash into astronauts' DNA, it can cause damage leading to
cancers or other radiation-induced illnesses. Images courtesy NASA's Office
of Biological and Physical Research.
Going one step further, layers of this structural material could be
laced with atoms of other elements that are good at filtering out other
forms of radiation: boron and lithium to handle the neutrons, and
aluminum to sop up electrons, for example.
Camping out in the cosmos
Earth's surface is mostly safe from cosmic radiation, but other planets
are not so lucky. Mars, for example, doesn't have a strong global
magnetic field to deflect radiation particles, and its atmospheric
blanket is 140 times thinner than Earth's. These two differences make
the radiation dose on the Martian surface about one-third as intense as
in unprotected open space. Future Mars explorers will need radiation
shielding.
"We
can't take most of the materials with us for a long-term shelter because
of the weight consideration. So one thing we're working on is how to
make radiation-shielding materials from the elements that we find
there," says Sheila Thibeault, a scientist at LaRC who specializes
in radiation shielding.
Right: Astronauts setting up
camp on Mars will need protection from space radiation. Image credit: Frassanito
and Associates, Inc.
One possible solution is "Mars
bricks." Thibeault explains: "Astronauts could produce
radiation-resistant bricks from materials available locally on Mars, and
use them to build shelters." They might, for example, combine the
sand-like "regolith" that covers the Martian surface with a
polymer made on-site from carbon dioxide and water, both abundant on the
red planet. Zapping this mixture with microwaves creates plastic-looking
bricks that double as good radiation shielding.
"By using microwaves, we can make these bricks quickly using very
little energy or equipment," she explains. "And the polymer we
would use adds to the radiation-shielding properties of the regolith."
Mars shelters would need the reliability of self-sensing materials, the
durability of self-healing materials, and the weight savings of
multi-functional materials. In other words, a house on Mars and a good
spacecraft need many of the same things. All of these are being
considered by researchers, Thibeault says.
The folks back home
Mind-boggling advanced materials will come in handy on Earth, too.
"NASA's research is certainly focused on aerospace vehicles,"
notes Anna McGowan, manager of NASA's Morphing Project (an advanced
materials research effort at the Langley Research Center).
"However, the basic science could be used in many other areas.
There could be millions of spin-offs."
|
'BigDog' Robot Joins U.S. Military
It
appears that DARPA (US Defense
Advanced Research Projects Agency) has been busy
since we last wrote about their research into
morphing metals. Their
latest invention is called 'BigDog', which is a
quadruped robot that walks, runs, and climbs on
rough terrain and carries heavy loads. BigDog is
powered by a gasoline engine that drives a
hydraulic actuation system. It's legs are
articulated like an animal’s, and have compliant
elements that absorb shock and recycle energy
from one step to the next. BigDog is the size of
a large dog or small mule, measuring 1 meter
long, 0.7 meters tall and 75 kg in weight.
BigDog is
being developed by Boston Dynamics with the goal
of creating robots that have rough-terrain
mobility that can take them anywhere on Earth
that people and animals can go.
Marc Raibert, the president of Boston Dynamics,
said: "Internal force sensors detect the ground
variations and compensate for them. And BigDog's
active balance allows it to maintain stability
when we disturb it."
Current models of BigDog are remote-controlled
from army bases by commanders. However it is
thought that future versions will be built with
eye-like sensors that allow it to become
"unleashed" by making intelligent decisions
about a journey. The program is
funded by DARPA.
For More Information
We were originally going to keep DARPA's
identity secret for a while for two reasons. The first reason was to keep this
story exclusive, and two, to stop other sites from simply going to DARPA and
beating us in releasing this interesting story that we have spent investigating
over the last 6 weeks. However, due to the wealth of information on the
DARPA site, and the lack of space on Cosmic Conspiracies server, we simply
cannot bring as much of the material that we would like to and therefore we have
decided to release the name of the main organisation involved so that you could
all check out the DARPA site for yourselves.
The URL is http://www.darpa.mil/
Also check out
http://science.nasa.gov/headlines/y2001/ast01mar_1.htm
CLICK ON THEIR SEARCH ENGINE ON
THE DARPA SITE AND TYPE IN THE WORD CHAP.
THERE ARE OVER 130 DOCUMENTS
WHEN WE LAST CHECKED, SO BE PREPARED TO STAY FOR A WHILE.
REMEMBER
WHERE YOU HEARD IT FIRST!
© Andy Lloyd, Dave and
Martin Cosnette
9th December 2001. Updated 10th February 2009
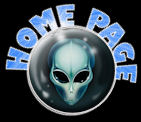